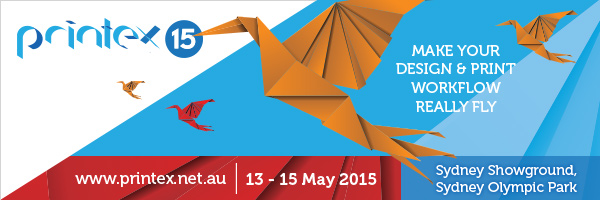
It's trade show time again!! Printex
15 is on 13th - 15th May at Sydney Showground, Sydney Olympic Park. Printex allows you to source the
latest products and services across all industry sectors, in one place at one time.
We are
excited to demonstrate our latest range of print finishing and laminating equipment. As the variety of
materials and products increase, we incorporate these technological advances directly into our machine
production. This results in superior, user-friendly machines without compromising quality or reliability.
At Printex, we will be showcasing the new Minibond
520 for the very first time and will demonstrate the popular Sign
Master Flatbed Applicator Table.
Also on display:
QLam
SAB-35
QLam
Iris
Sign
Master 1600
Lami
Trim LS1300 Trimmers
Our staff look forward to discussing your
laminating requirements. Whether you are after solutions for digital or offset print, entry level or large
automatic machines for a small copy shop or large print house we have you covered. The benefits of being
trade service providers are that Lamination System are able to offer our clients practical advice and
experience in all areas of film lamination. Deal with the experts in all areas of celloglazing, encapsulating,
wide-format, cold laminating and mounting and experience the benefits for yourself.
Take
advantage of over 20 years experience and come see the Lamination Specialists at stand 2723!
The Mini
Bond 520 Celloglazing Machine is a proven solution, allowing easy lamination for digitally and offset
printed applications up to 485mm wide.
This compact machine has a convenient one person
operation with an accurate belt fed system, built in de-curl unit and rewind drum.
This
520mm wide machine has been designed to laminate SRA3 sheets landscape, resulting in increased efficiency
and high quality finish.
Capable of single and double sided celloglazing, the Mini Bond 520
is perfect for laminating business cards and covers and a great addition to any print room.
Features Include:
-
Large diameter chrome hot roller with smooth and efficient
heating
-
Designed to laminate SRA3 sheets landscape
-
Built in rewind unit
for single person operation
-
Perforation wheel for ease of separating laminated sheets
-
Adjustable de-curl unit
-
Open and close rollers
-
Belt feed system
for easy overlap and sheet guide
-
Single and double sided laminating
-
Remote
foot control
-
Mini commercial features
-
Variable temperature control
Want to see one in action? Check out our video
page, subscribe to us on YouTube
or phone 1300 099 030 to arrange a demonstration today!
Tech Tips
Sticking to Digital Print
The most common question
we get asked by printers is "How do I stick to my digital print?"
With technology
constantly changing and finishing struggling to keep up, we have established four key points in gaining
the best adhesion possible to all digital print.
Machinery:
In order to gain sufficient heat and pressure to stick to your digital output, it is essential
your celloglazing machine has a large diameter chromed heating roller. The larger the diameter of
the chrome roller, the greater the contact area is and the faster you can laminate.
To
gain speed from this process your machine must also have compressed air.
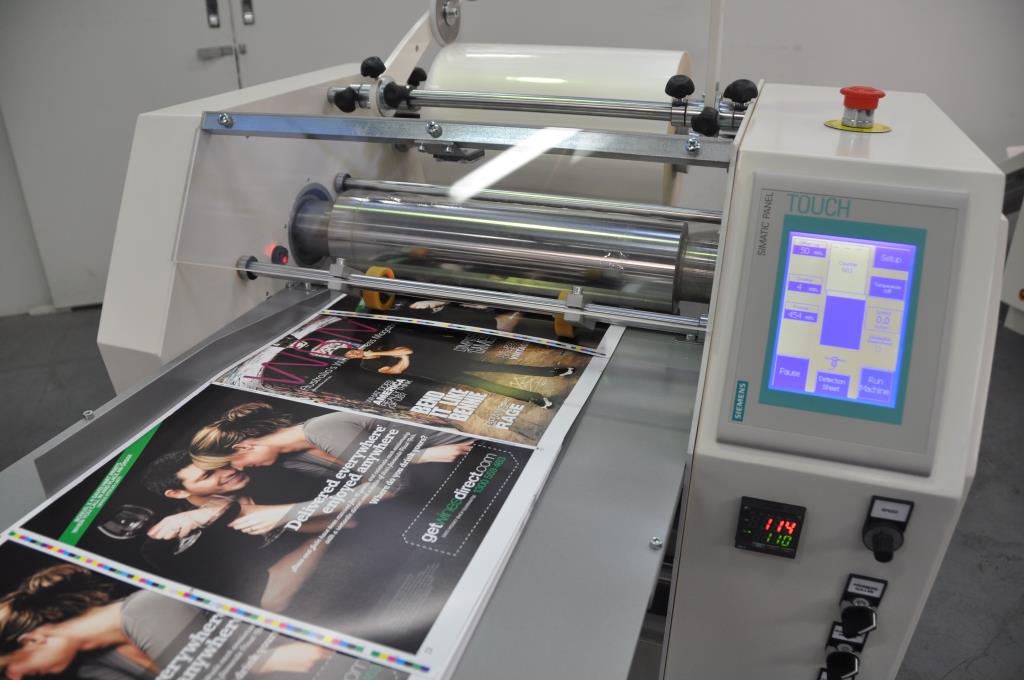
Temperature:
Finding the perfect temperature for laminating
is trial and error, as all machines vary slightly in calibration and all films vary in processing temperatures.
Ensure your machine has sufficient warm up time which for most desktop laminators is around
20-30 minutes. The temperature needs to be between 110 C and 120 C and always sacrifice the 3rd
sheet to test adhesion by scoring and roughly cutting at the surface.
You may need to
increase the temperature slightly while you are running your job, as constantly laminating will draw heat
out of the machine. Just remember to reduce the temperature again when you are finished!
If the machine is too hot, the film will crease and shrink towards the centre. Turn it down
a little, wait 10 minutes for it to respond and start again.
Speed:
As a rule, digital output needs to be laminated at slow speed. The heavier the toner, the
slower the processing speed. With the only exception being a machine with a large diametre, chromed heating
roller and compressed air as discussed.
If you increase or alter your speed while laminating,
always remember to re-check the adhesion level. It may seem time consuming to laminate digital print properly,
however it saves time in the long run by not having to reprocess or reprint your job!
Film:
Probably the most important point, different
digital print requires different film.
Establishing your output will determine the best
film for the job, or when in doubt, do as we do and just run our Premium
Digital BOPP 45 Micron as we know it sticks to everything!