|
July- September 2015
Issue No. 6
Inside this issue
Follow up from Printex
Product Profile: LEDCO from U.S.A
Tech Tips: how to set your roller pressure
Matts Wrap: Encapsultors: heatshoe or hot roll?
Staff Profile: Sarah
Smith
Our Staff
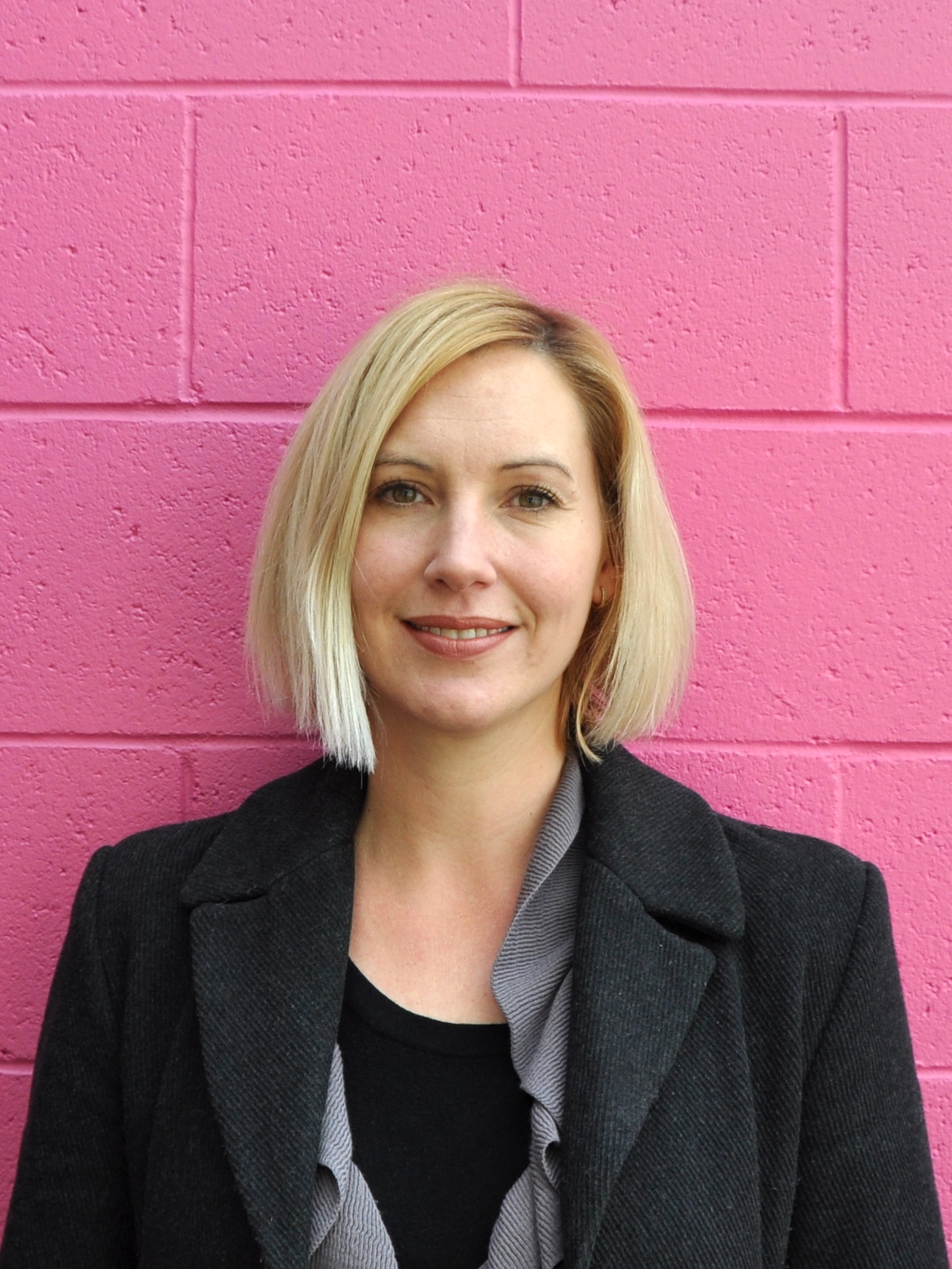
Meet Sarah Smith...
There is no need for an introduction, we assume you all
know Sarah well.
Reluctantly admitting to over 20 years of industry experience, she finds herself
picking apart menus at restaurants and fault finding in every coated surface she comes across.
When she is not at work selling machines and solving laminating problems, her favourite thing is her
garden in the hills, her stupid fluffy dog Molly and caravanning with her husband and kids.
Well known at work as the master of delegation, she is just as happy working on the factory floor
as she is dressed up on the trade show floor, enjoying the banter and familiarity of the printing industry.
Matt's Wrap:
Encapsulators:
heatshoe or hot roll?
When
it comes to encapsulation, people often get confused by the differences between a heat shoe machine and
a hot roll laminator.
Encapsulation is thermal polyester lamination on both sides of the sheet,
to create strength and often an encapsulated seal around a document such as a menu or poster.
Heat shoe laminators heat the rollers externally and the laminate is heated and melted on the heat
shoe prior to the enclosed rollers applying it. This enables greater speed for polyester encapsulation,
and is the most common form of roll laminator.
Hot roll machines require the internally heated
roller to melt the glue as it applies it. While this reduces scratching, it also reduces production speed
by over half.
Either way your rollers and heat shoes need to be spotlessly clean, as any residue
or marks on the heat shoe or roller will scratch the film or foot print on to the laminated surface.
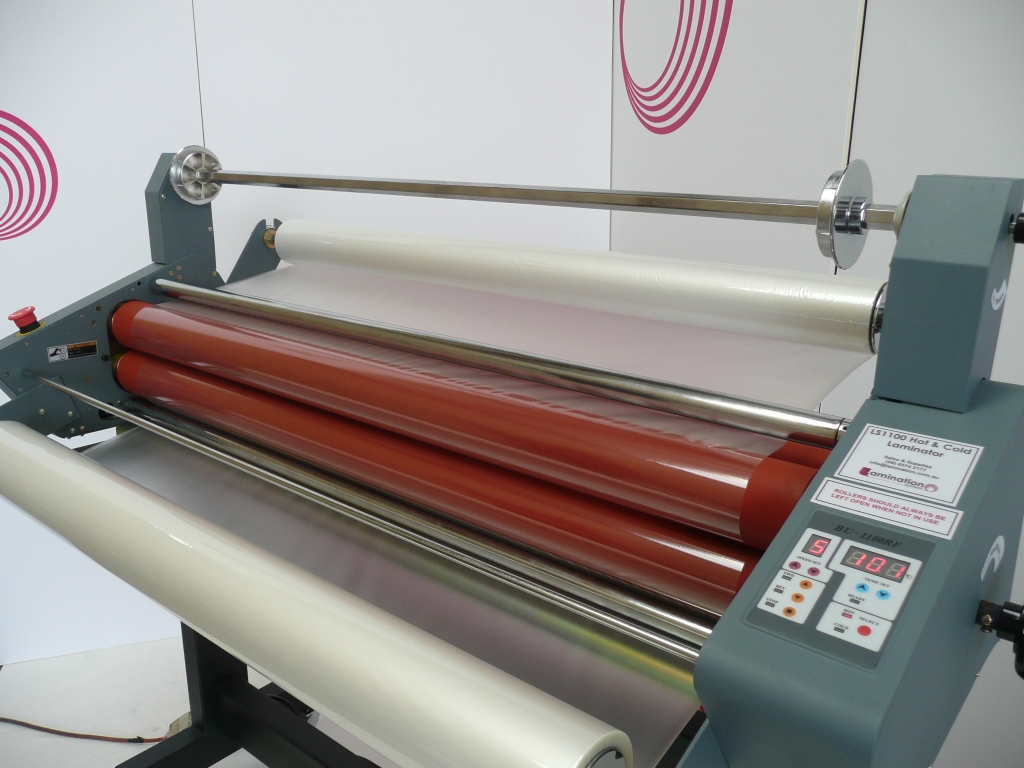
LS1100
Hot Roll Machine
Next Issue
2016 Wall Planners
Product Profile: QLam Iris Series 2
Tech Tips: Setting Roller Pressure on Cold Laminators
Matts Wrap: Papua New Guinea
Machine Installation
Staff Profile: Meet the Director!
We hope you enjoyed our latest newsletter!
If you have any feedback or
topics you would like us to include, please contact us on info@lamination.com.au
|
|
|
NEW!!! Sky Pouch Machines
Sky 335R6
We have sold the last of the popular Peach 3500
machines and are happy to announce the arrival of its replacement... the Sky
335R6. This high speed, heavy duty Pouch Machine is designed for high volume use and will achieve
photo quality, professional results every time. Check out the manufacturer's video here
and contact us for
more information.
Features:
-
6 rollers for increased volume capacity
-
4 internally heated rollers
with anti-jam coating
-
Digital temperature and speed control
-
Reverse
function
-
LCD display
-
Preheat mode
-
Standby and auto
power off function
-
Easy to clean
-
High speed performance
-
No carrier required
-
12 months parts warranty
Sky 330R4
Sky Laminators offer excellent value for money results,
with a range of laminators for low volume use through to high speed professional machines.
For
schools, businesses, photo labs, copy shops and home, we have a Pouch Laminator perfect for your laminating
needs, including the Sky
330R4.
Features:
-
4 rollers (2
internally heated)
-
Reverse function
-
Variable temperature control (0-150
degrees)
-
Preheat mode
-
Standby and auto power off function
-
Easy to clean
-
High speed performance
-
No carrier required
-
12 months parts warranty
Review of Printex 2015
Print Ex is held every four years as a merged trade show, combining and showcasing the latest
in digital print with Visual Impact and wide format.
This May, we all made the trek out
to Sydney Olympic Stadium and were pleasantly surprised at the quantity and quality of enquiries.
Proving again that the industry is moving further and further towards wide format, the show highlighted
just how much wide format equipment is out there and the variety of products and finishes that can be
achieved easily.
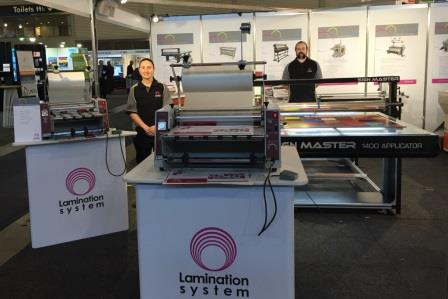
As anticipated, our new Minibond
520 was a success, selling out before the end of financial year and the Sign
Master Applicator gained plenty of attention as well, for being the most robust, user-friendly applicator
on display.
The AGSA Wrap Master Challenge once again proved a hit, and this time around
we gained a mention as a key sponsor through our preferred distributor Australian Visual Solutions.
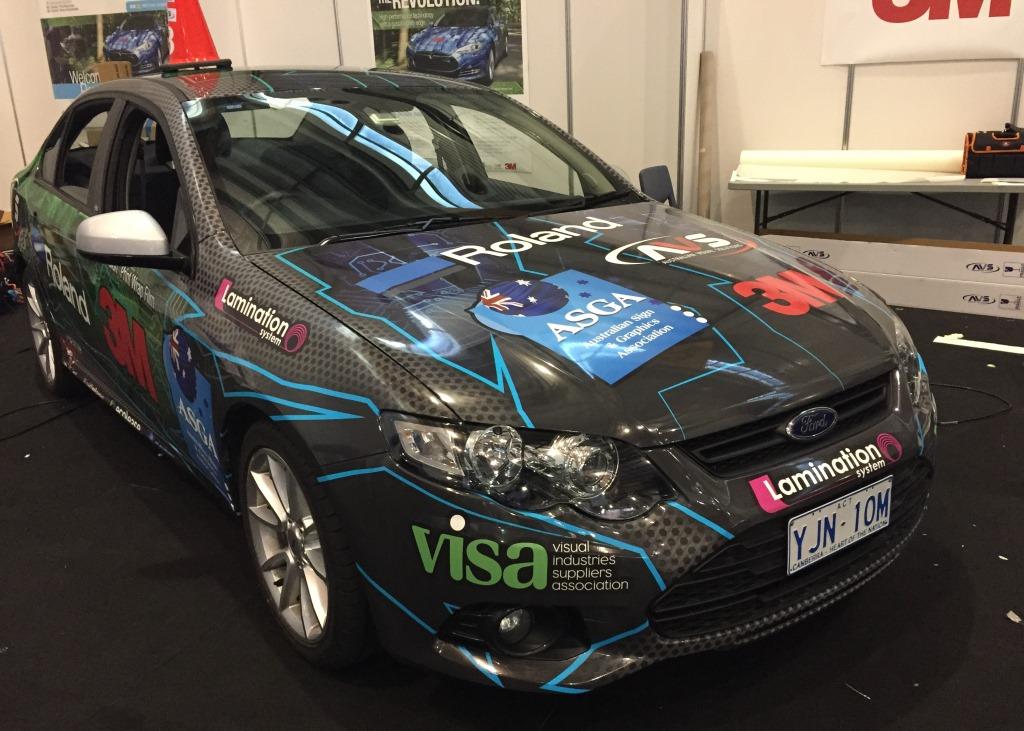
Product Profile: LEDCO
Last month we imported our first LEDCO
High Speed Laminator in 20 years!
Built in the USA these machines are heavy duty and
robust beyond anything the Australian market has seen.
These machines complete our industrial range as high speed, double sided encapsulators.
We have had our LEDCO Workhorse laminator in our factory for 24 years and it is still going
strong. With accessories such as Chill Rollers (for high speed), Auto Feed and Auto Cutters, this
range has been designed for high volume encapsulating and the trade professional.
For more information check out:
Tech Tips: Setting
the Roller Pressure on a Thermal Laminator
The best way to check the roller pressure on a thermal machine it to test it while the machine
is hot and webbed up with film.
With the rollers closed, feed in a dark sheet (full width)
and let the sheet sit in the nip of the rollers for around 20 minutes. When you then feed it out the back
you should find 2 parallel lines indicating even pressure across the rollers.
If the lines
widen towards one side, you may need to either take some pressure off that side or apply more pressure
to the opposite side to make it even.
Many machines such as the MiniBond,
you can adjust the pressure externally on the unit, however remember to just do small adjustments at a
time and less pressure is best when it comes to laminating.
Next time we discuss how to set
roller pressure on a Cold
Laminator.
|